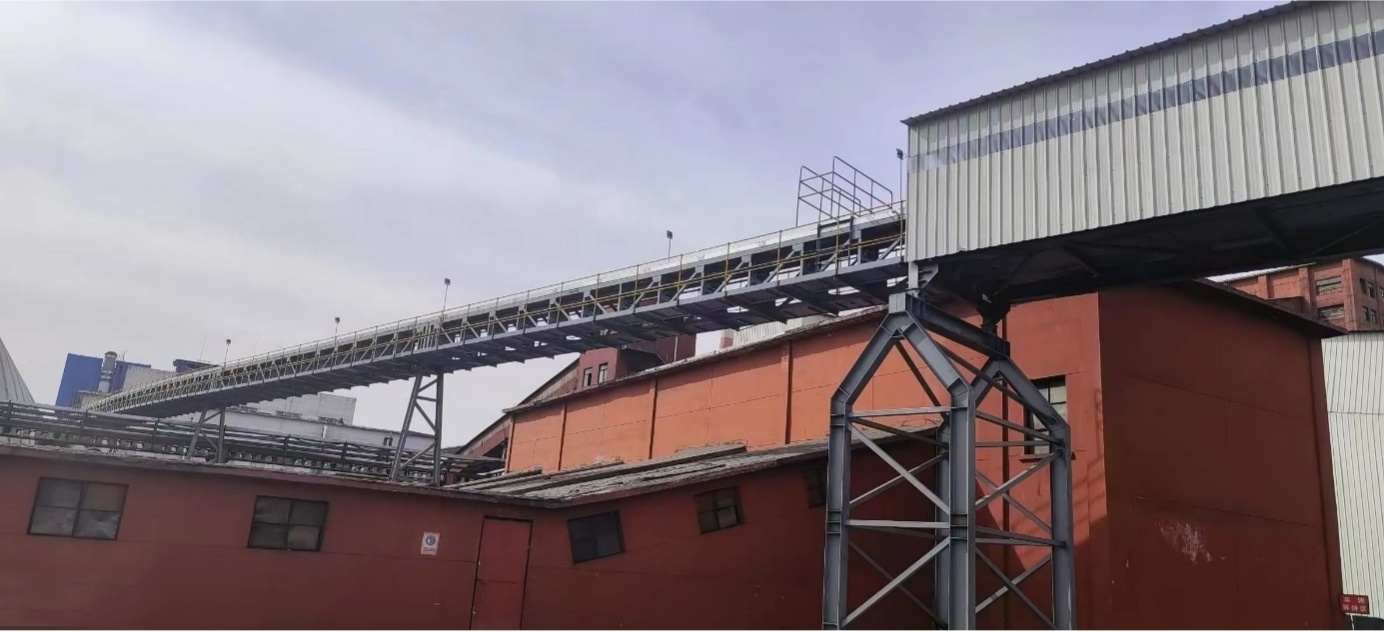
Multi-point unloading in close proximity to each other
When the two unloading points are close to each other and in the same straight line position,the following design and processing methods can be used:1.Belt unfolding structure:unfold the belt as early as possible before the first unloading point,and add a pair of unfolding pressure rollers in the transition section to the groove arrangement to prevent the belt edges from curling,to ensure that the materials can be smoothly discharged from the belt,without affecting the unloading effect because of the curling of the belt edges.
2.Roller Configuration:Adopt standard 35 degree groove angle rollers to provide good support,or use special adjustable transition rollers for pipe belt machine and adjust them according to the specific conditions to ensure that the belt remains stable in the process of unloading.
3.Convex arc processing:If there is a convex arc at the head of the pipe belt machine,the transition section should be arranged at the front end of the convex arc to ensure that the convex arc section is a groove-shaped structure,reducing the bending radius required to avoid excessive bending of the belt in the convex arc section,which affects the normal conveying and unloading of materials.
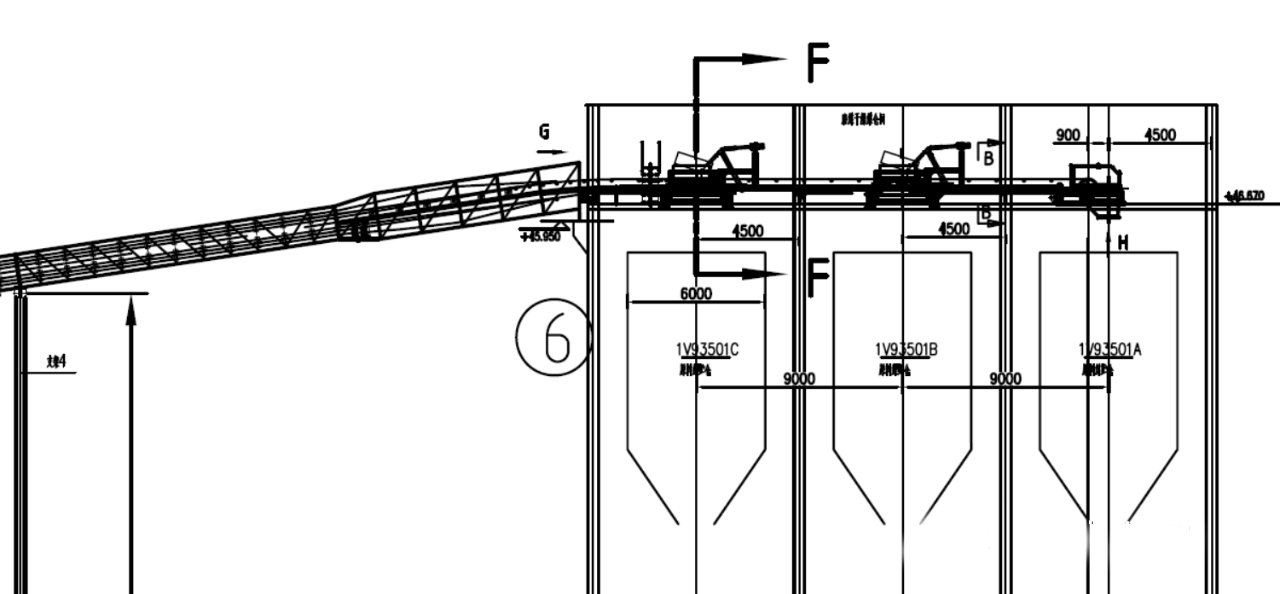
the long distance between the multi-point unloading
When the two unloading points are far away from each other(more than 3 times the length of the transition section)and the middle involves a horizontal turning point,the following programs can be used:1.Unloader unloading:reopen the tape at the middle unloading point and unload through the plow unloader.This method requires additional spreading pressure rollers before and after the unloading point to prevent the belt from curling.It ensures that the material can be discharged smoothly even over long distances without the material piling up on the belt due to long distances,and is suitable for conveying less abrasive materials such as coal and powders.
2.Fixed unloading truck type tee unloading:two redirecting rollers and a head hopper are set in the middle unloading point,and the bearing section of the pipe belt machine is elevated.This method is suitable for any scenario,especially for materials requiring high breakage rate requirements.The angle of inclination of the branches of the carrier section should be taken as much as possible to the maximum permissible conveying angle of the material in order to reduce the space arrangement and investment cost.In this design,the tape in the carrier section of the pipe belt machine needs to be reopened at the discharge point,and then formed into a pipe again after winding around the two redirecting rollers,or choose not to be formed into a pipe again.
3.Segment way tee unloading:the whole conveyor line is divided into several belts according to the number of unloading points to realize multi-point unloading.It is suitable for the situation that the head unloading place needs to be unloaded by mobile unloading truck within a certain length range,or the middle unloading point is at the horizontal turning point.By adding transfer station at the turning point,the conveying line can be divided into several belts to realize flexible multi-point unloading.
about the sealing of the unloading point
The environmental protection characteristics of the pipe belt machine are mainly reflected in the pipe forming part,and the unfolding part of the multi-point unloading needs special consideration for environmental protection sealing.Specific sealing measures are as follows:1.Sealing of multi-point unloading through the unloader:in accordance with the conventional treatment,make a closed pass-through corridor,and increase the dust removal facilities at the unloading to prevent the dust from spreading and affecting the surrounding environment.
2.Central fixed unloading truck unloading and segmentation to increase the transfer station unloading sealing:the transfer station is completely closed,the transition section also needs to be closed,and increase the dust removal facilities at the unloading,can effectively prevent the material in the unloading process scattered and dust diffusion,to ensure a clean environment.
3.Specific implementation of sealing measures:in the implementation of sealing measures,need to be adjusted according to the specific circumstances.For example,in the vicinity of the unloading point can be set up to close the corridor and dust removal facilities to ensure that the material in the unloading process will not produce a lot of dust.In addition,suitable sealing materials and equipment can be selected according to the characteristics of the material to ensure the best sealing effect.